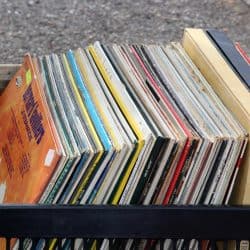
How Vinyl Records Are Pressed and Perfected
Vinyl is having a serious comeback, but making a record is more hands-on than most people think. Here’s a behind-the-scenes look at the craft, care, machines and how vinyl records are pressed.
How Vinyl Records Are Pressed, and Perfected
by Philip Kinsher via Disc Makers Blog
Several decades ago, who would have predicted the resurgence of vinyl, let alone that vinyl albums would once again outsell CDs? Audiophiles, collectors, and casual listeners alike are drawn to the analog warmth of vinyl and the tactile nature of vinyl jackets. It’s a format that offers both charming nostalgia and a unique, high-quality listening experience.
As demand grows, understanding the complex, hands-on process of making a vinyl record — from mastering to pressing — is more relevant than ever. So, let’s explore how modern records are made with both vintage artistry and precision engineering.
Table of Contents:
• The mastering process
• Lacquer cutting
• Electroplating and creating the stamper
• Introduction to record pressing
• Quality control: ensuring audio fidelity
• In conclusion
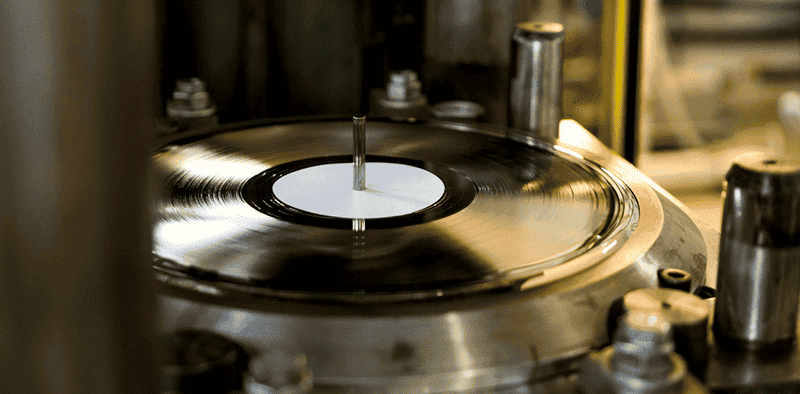
The mastering process
Before a vinyl record can be pressed, the music first has to be mastered for the format.
What is mastering?
Mastering is the final step in audio post-production. It ensures that a recording sounds cohesive and polished while also being optimized for the intended playback medium. So, if you are planning to release music on CD, vinyl, and streaming, you will have to create three different masters.
Vinyl mastering is a particularly critical process that cannot be overlooked. Unlike digital formats, vinyl has physical limitations that affect how audio should be prepared. Without careful mastering, a great recording can translate poor
Mastering for vinyl is about more than just volume maximization or EQ correction — it’s about preparing the music to behave predictably and beautifully when carved into grooves.
Digital vs. analog mastering
Although many modern recordings are tracked and mixed digitally, the mastering stage offers a couple of options. So, should you master digitally or go analog?
Digital mastering is more accessible and flexible, using software to analyze and adjust audio. Analog mastering, however, uses hardware — like EQs, compressors, and tape machines — which many engineers believe produces a warmer, more natural sound.
At the end of the day, there is no one answer for every release. The choice of analog or digital mastering will depend on your music and its specific needs.
When preparing a vinyl release, even if digital tools are used, the engineer must tailor the sound for analog playback. This includes limiting excessive sibilance, adjusting phase relationships, and controlling extreme frequencies.
Frequency and dynamic range considerations
Vinyl can’t handle extreme low-end or very bright, high frequencies the same way digital formats can. Excessive bass — especially if it’s stereo rather than mono — can cause the needle to jump out of the groove. Likewise, very high frequencies can result in distortion or groove damage.
Dynamic range also plays a critical role. While vinyl supports impressive dynamics, overly compressed masters can backfire. A well-mastered vinyl cut balances dynamic musical expression with the mechanical needs of the format.
To get a perfect mastering for your custom vinyl record, trust a professional, like the engineers at The SoundLAB at Disc Makers.
Lacquer cutting
Once mastering is complete, the audio is ready to be physically transferred onto a lacquer disc. This process is known as cutting and is the first step in creating a physical representation of the soundwave.
Overview of the lacquer cutting process
Lacquer cutting transforms the digital or analog audio into a modulated spiral groove etched into a lacquer-coated aluminum disc. This groove represents both the amplitude and frequency of the audio signal.
Equipment used in lacquer cutting
The heart of the process is the disc-cutting lathe. This is a precision machine that uses a heated stylus to engrave audio-modulated grooves onto a blank lacquer disc. Brands like Neumann, Scully, and VMS are known for their reliability and quality in this field.
A cutting engineer monitors real-time audio levels and groove modulation during the process. The stylus must remain perfectly balanced and sharp, while the platter rotates with clockwork precision at 33 ⅓ or 45 RPM.
Wondering what a lathe actually looks like? Step inside the Disc Makers factory just outside of Philadelphia and take a look for yourself:


The importance of groove geometry
Groove geometry determines playback fidelity. The width and depth of each groove must correspond to the amplitude of the sound. Louder passages require wider grooves, while quieter passages require narrower ones.
Spacing is also dynamic. The lathe adjusts the groove width in real time based on signal amplitude. Poor groove geometry can result in tracking errors, distortion, or skips during playback.
All of which is to say that you want a lacquer cutting pro, like the experts at Disc Makers, to make your lacquer.
Electroplating and creating the stamper
A lacquer disc cannot be played more than a few times without degrading. So instead, it is used to create a metal mold through a process called electroplating. This step allows the mass production of records from a single original master.
Electroplating chemically transfers the groove pattern from the soft lacquer onto a durable metal surface — usually nickel.
Creating the metal master
The lacquer disc is first coated with a layer of silver nitrate to make it electrically conductive. It is then submerged in a nickel bath where electroplating occurs. Nickel ions are deposited onto the lacquer surface, creating a negative metal version called the “father.”
This father has ridges where the lacquer had grooves — essentially a mirror image of the record.
The production of the stamper
From the metal father, a “mother” (positive) can be made, which is an exact replica of the original lacquer. From this mother, multiple “stampers” (negatives again) are created. These stampers are what will be mounted in pressing machines to physically create the final vinyl records.
Stampers must be precise, durable, and free of defects to ensure high-fidelity pressing.
Introduction to record pressing
Once stampers are ready, they’re installed into record presses — large hydraulic machines that form the records using heat and pressure. This step involves shaping raw vinyl pellets into playable discs.
Producing the vinyl pellets
Vinyl records are typically made from polyvinyl chloride (PVC). Pellets are either virgin (pure) or recycled (from trimmed waste or unsold records). Virgin vinyl produces higher-quality audio with fewer surface noises, while recycled vinyl is more environmentally friendly, but may contain contaminants.
Vinyl also comes in various colors and compositions. Black is most common due to its carbon content, which improves durability, but colored, marbled, and splatter-printed vinyl is popular among collectors.
Importance of vinyl composition
The purity, flexibility, and melting properties of vinyl pellets affect the final sound quality. A well-formulated blend ensures the grooves capture fine detail and the record lasts through repeated plays without degradation.
Not only does the composition of the vinyl affect the sound, but so does the weight. Most albums are either 140 or 180 grams. If you want a premium experience, choose 180 grams for your release, as heavier records can offer increased durability.
Pressing the record
Pellets are heated to a molten state and formed into a “biscuit” or “puck.” This soft lump is centered between the two stampers.
Using the stamper in pressing
With labels already placed on either side, the press closes around the biscuit. High pressure and heat force the stampers into the vinyl, molding the grooves into the disc’s surface. Pressing takes just a few seconds per record.
Cooling and trimming
Once pressed, the record is quickly cooled using water or air jets to solidify the shape. Excess vinyl (called “flash”) is trimmed from the edges, producing a clean, round disc ready for packaging.
Quality control: ensuring audio fidelity
Each step of the vinyl manufacturing process must be tightly controlled to ensure the final product meets audio and aesthetic standards. This begins with test pressings — small batches made before full production — to identify any potential issues in sound or surface quality.
Test pressings are carefully evaluated for frequency response, noise floor, stereo imaging, and overall fidelity.
Visual inspection and testing
Each finished record is visually inspected under light to identify warps, scratches, and non-fill (areas where vinyl hasn’t properly filled the groove), as well as surface and edge defects. Surface sheen and evenness also indicate quality.
Audio testing for consistency
Sampling from each pressing run is standard. Selected records are played back in real-time by quality control technicians to verify that no groove damage, skips, or distortion has occurred.
Consistency is key — a good pressing plant will maintain tight tolerances in temperature, pressure, and timing throughout the run to minimize variability.
Want to see the vinyl presses in action? Check out this short video on our YouTube channel:
In conclusion
Vinyl manufacturing is as much art as it is science. Every record passes through a complex chain of analog craftsmanship — from mastering and lacquer cutting to electroplating and pressing — each stage requiring precision, expertise, and careful quality control. While modern technology has streamlined parts of the process, the fundamental methods remain rooted in techniques perfected over decades.
The recent vinyl revival is more than a trend — it’s a testament to the lasting value of a premium product that offers listeners a premium experience and collectors a gorgeous, tactile work of art. For musicians, collectors, and fans alike, vinyl offers an immersive audio experience that digital simply can’t replicate. And behind every record lies a story — not just in its grooves, but in the hands and machines that brought it to life.
To release your own custom manufactured vinyl album, be sure to contact the vinyl professionals at Disc Makers, who began making vinyl back in 1946, so you know your music will be in good hands.
Philip Kinsher is a writer, editor, and musician with a predilection for YA Sci-fi Fantasy books and rock and roll. And golf and pickleball.